Value Added Services
Efficiency, Cost-Effectiveness and Quality in Every Turn
Lower manufacturing costs, shipping costs and accelerate production timelines with our full suite of value-added services. Jet Donald Plastic Injection & Bakelite Manufacturing provides a wide range of value-added services for plastic injection molding, designed to enhance efficiency, reduce costs, and maintain strict quality standards for products that consistently meet your expectations.
At Jet Donald Plastic Injection & Bakelite Manufacturing, your entire project moves seamlessly from one workstation to the next, all under one roof. This not only saves on shipping and packaging to multiple sites but also shortens timelines and ensures superior standarized quality control. Rely on our value-added services for a streamlined, efficient production experience.
Please see our list of value-added services below:
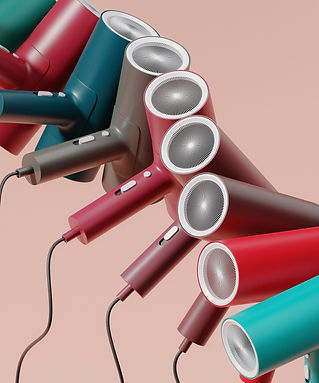
See Our Services
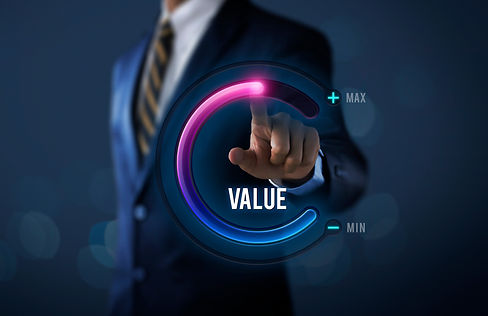
Contract Manufacturing
Cost Savings: Eliminates the need for companies to invest in expensive equipment.
Expertise and Specialization: Leading to higher quality products and efficient production processes.
Speed to Market: Expedite production timelines, helping companies bring products to market faster.
Quality Control: Follow strict quality standards and certifications, ensuring consistent quality and compliance with industry regulations.
Risk Reduction: Mitigates the risks associated with machinery maintenance, staffing, and production issues.
Supply Chain Efficiency: Streamline the procurement of raw materials and components, reducing lead times and costs.
Reduced Labor and Management Burden: Minimizes the need for hiring, training, and managing a production workforce, allowing companies to operate more leanly.

Printing / Painting
Printing on plastic plays a vital role in modern manufacturing and packaging. Achieving high-quality results requires specialized techniques and expertise to ensure optimal performance and durability. We offer the following processes:
Digital InkJet printing
Screen printing
Flexo printing
UV Litho printing
Pad printing
Hot Stamping
EMI / RFI Shielding / Electroplating
Essential for protecting electronic devices from electromagnetic and radio frequency emissions. In plastic enclosures, EMI/RFI shielding can prevent interference from affecting the performance of internal or nearby electronic components. We can assist choosing the best method for your needs.
Conductive coatings
Electroplating
EMI/RFI Films
Plated Plastic Inserts
Conductive Compounds
In-Mold Labeling with Conductive Materials


Thermal Heat Staking
A process used to join plastic components or plastic to metal by applying localized heat and pressure. This method is favored for its ability to produce strong, permanent joints with minimal environmental impact, as no solvents or additional fastening elements are required.
Key Features of Thermal Heat Staking:
Precision
No Need for Additional Materials
Strong, Reliable Joints
Versatility
Efficiency
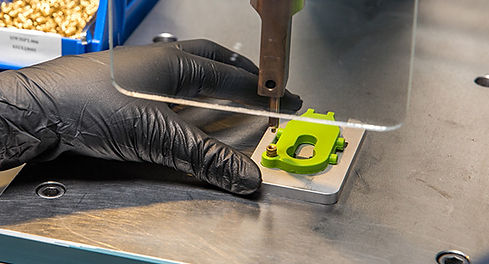
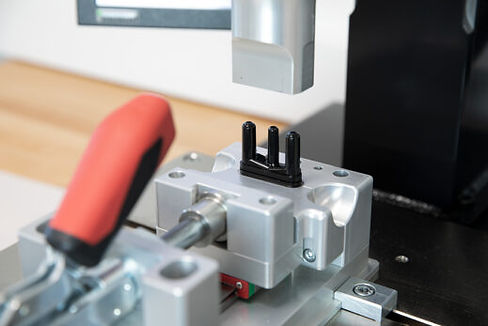
Ultrasonic Welding
Ultrasonic Plastic Welding (USW) is a process used to join or reshape thermoplastic materials using heat generated from high-frequency mechanical vibrations. In this technique, high-frequency electrical energy is first converted into mechanical motion. This motion, when combined with applied pressure, produces frictional heat at the interface of the plastic parts (known as the joint area), causing the material to melt. Once melted, the plastics form a molecular bond as they solidify, resulting in a strong joint between the components.
Insert Molding
Insert molding is a plastic injection molding technique that involves placing a pre-made insert into a mold cavity and then injecting molten plastic around it. The insert becomes a part of the finished product, and the two materials form a strong bond.
Insert molding is used to create a variety of products, including:
-
Metal attachment features: Fasteners, such as threaded inserts, can be molded into plastic to create secure attachment points.
-
Insulated pipes and wiring: Insert molding can be used to create insulated pipes and wiring.
-
Electronics in plastics: Electronics can be embedded into plastics using insert molding.
-
Plastic handles on metal tools: A plastic layer can be added on top of a metal tool, such as a screwdriver, to create a plastic handle.

Custom Packaging
If your products requires special or custom packaging during transit, we can cater to your needs in order to protect and market your products better.



Assembly and Kitting
Assembly and kitting play an essential role in creating a lean, efficient production process. They support quality control, reduce errors, improve inventory management, and lead to quicker and more reliable fulfillment times, enhancing both operational efficiency and customer satisfaction.
1. Assembly Benefits
Reduced Production Time
Quality Control
Improved Inventory Management
Customization Options
Cost Savings
2. Kitting Benefits
Enhanced Operational Efficiency
Reduced Assembly Errors
Decreased Handling Time
Lower Storage Costs
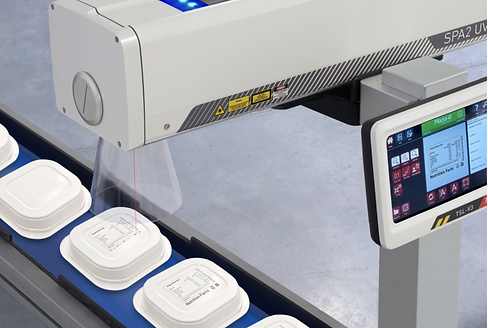
Laser Markings
Laser printing, or plastic engraving, is a non-contact printing technique that uses a laser to label or mark components. This method delivers high-quality, precise, and detailed prints with sharp lines, even for small or intricate designs. Since it’s a non-contact process, there is no physical interaction with the plastic material, reducing the risk of damage.
One of the key benefits of laser printing is its cleanliness and environmental friendliness. Additionally, it generates less waste compared to traditional printing methods, as it only melts the surface of the plastic rather than adding layers of ink or other materials.
Surface Finishes
Plastic surface finish is essential in product design, enhancing both aesthetics and functionality. A well-chosen finish can transform a product from basic to outstanding and can also conceal imperfections like flow lines or sink marks from the injection molding process. Additionally, textured surfaces improve paint adhesion and ensure a better grip and feel for the user. The right surface texture completes the product, making it look polished and professional.

Mold Flow Simulation and Analysis
Mold flow simulation and analysis is a software-based technique that predicts how a plastic resin will flow into a mold during the injection molding process:
Benefits of mold flow simulation and analysis
Helps avoid defects
Saves time and money by allowing changes to be made before cutting a tool
Material selection
Helps optimize process settings, cooling efficiency, and feed system designs
Gate positioning
Knit lines
Helps locate spots in the mold that are difficult to fill
Helps examine how resins flow at different temperatures and injection pressures
Helps account for part cooling
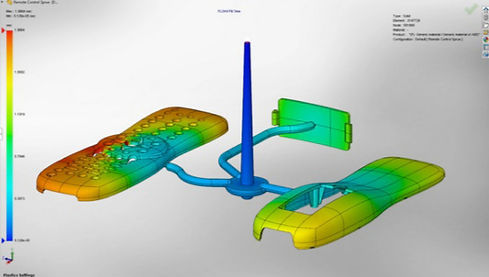
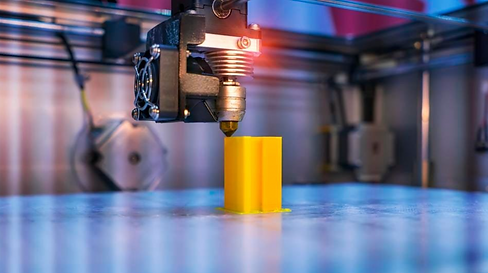
3D Printing
3D printing helps plastic injection companies by speeding up prototyping, enabling flexible tooling options, lowering costs, and supporting sustainable production practices, making it a valuable tool in modern plastic injection operations.
3D Printing offers the following benefits:
1. Rapid Prototyping
2. Tooling and Mold Production
3. Enhanced Product Development
4. On-Demand Spare Parts and Jigs
5. Sustainability
We offer two of the most established types of 3D printers for plastics parts: stereolithography (SLA) and selective laser sintering (SLS)
Benefits
Jet Donald Plastic Injection & Mold Design's value-added services bring several benefits for our customers. Here are some core values Jet Donald can provide:
Cost Reduction: By offering additional processes (assembly, finishing, or packaging) under one roof, value-added services reduce the need for third-party vendors, minimizing shipping, handling, and packaging expenses.
Efficiency and Speed: Integrated value-added services enable a smoother, faster transition between production stages, reducing lead times and ensuring quicker project completion. This accelerates time-to-market, which is crucial in competitive industries.
Quality Control: With all services centralized, manufacturers can better monitor and manage quality across each stage, maintaining higher standards and consistency throughout the production process.
Streamlined Logistics: Centralized services simplify logistics by reducing the complexity and costs associated with coordinating multiple suppliers or locations.
Customization: Value-added services enable greater flexibility for customizations, such as specific assembly, finishing touches, or packaging requests, to create a product that meets specific customer needs.
Risk Reduction: Consolidating services minimizes the risks associated with multiple handoffs, which can lead to errors, delays, or damage in transit.
Enhanced Customer Experience: With a streamlined and controlled process, customers receive a faster, high-quality product that aligns with their exact specifications, strengthening their confidence and satisfaction.
By integrating these services, Jet Donald Plastic Injection & Mold Design offer clients a more seamless, efficient, and cost-effective production experience.